For all applications.
Whether photovoltaic systems for private homes, businesses or solar parks - with solar modules from IBC SOLAR you will find the perfect solution for your requirements.
We rely on excellent material combinations with innovative cell and module technologies, always at the cutting edge of technology, such as the IBC SOLAR half-cell modules (half-cut).
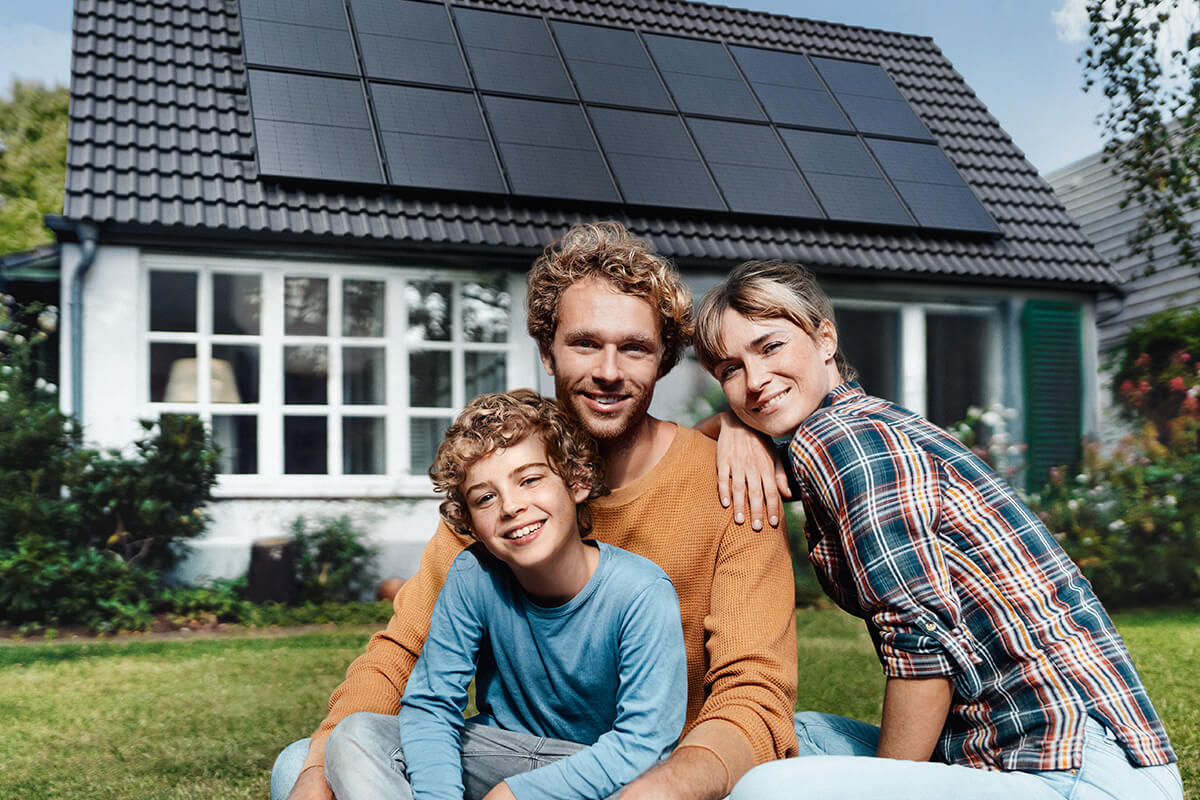
This is what solar modules from IBC SOLAR offer.
- German guarantor & 25-year performance guarantee
- High efficiency
- Visually uniform cell colours
- Simple installation thanks to long connection cables
- Optimum low-light behaviour
- Unique quality assurance measures
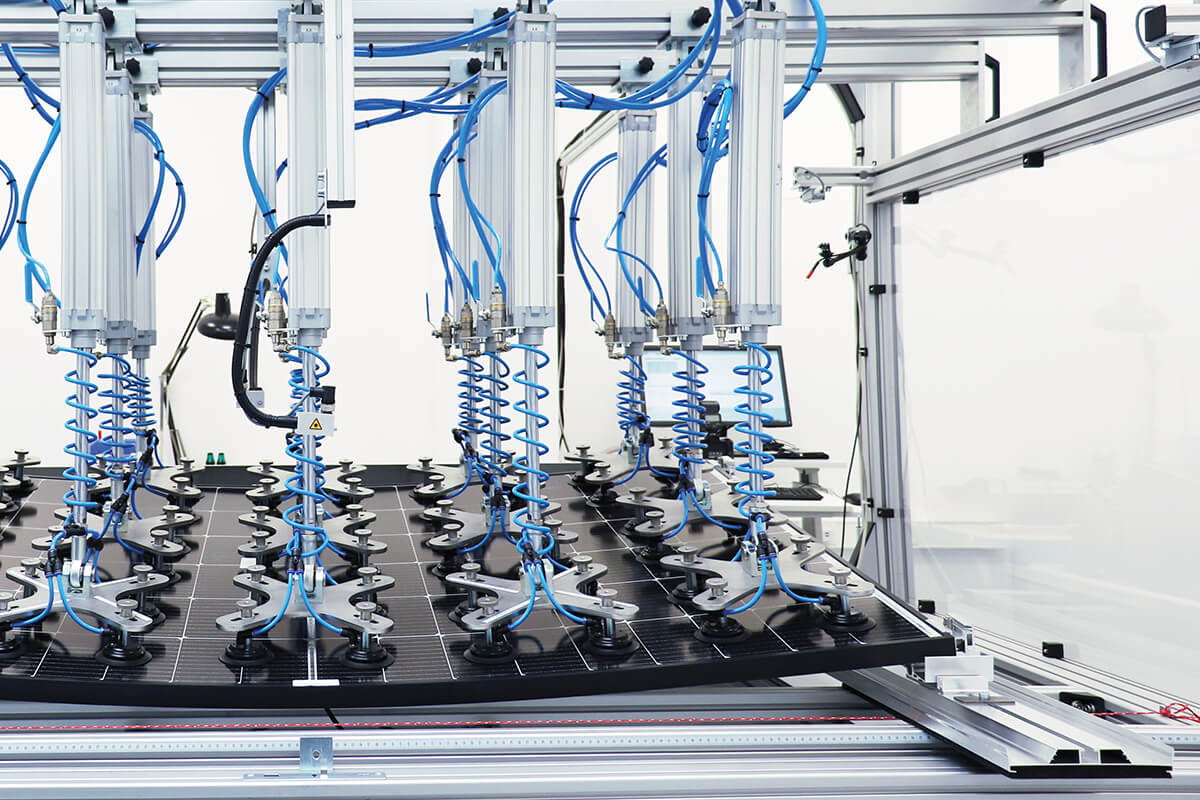
Top quality module for module.
The attractive half-cell modules (half-cut) from IBC SOLAR are characterised by high efficiency and a positive power tolerance of up to 5 watts. As a German warranty provider, IBC SOLAR offers guaranteed performance for a period of at least 25 years. Our quality measures are unique in the industry: starting with the qualification of suppliers through to 7 endurance tests in the SUNLAB PV test laboratory. This means we can be sure that our modules deliver what they promise and that they provide maximum energy yields at all times.
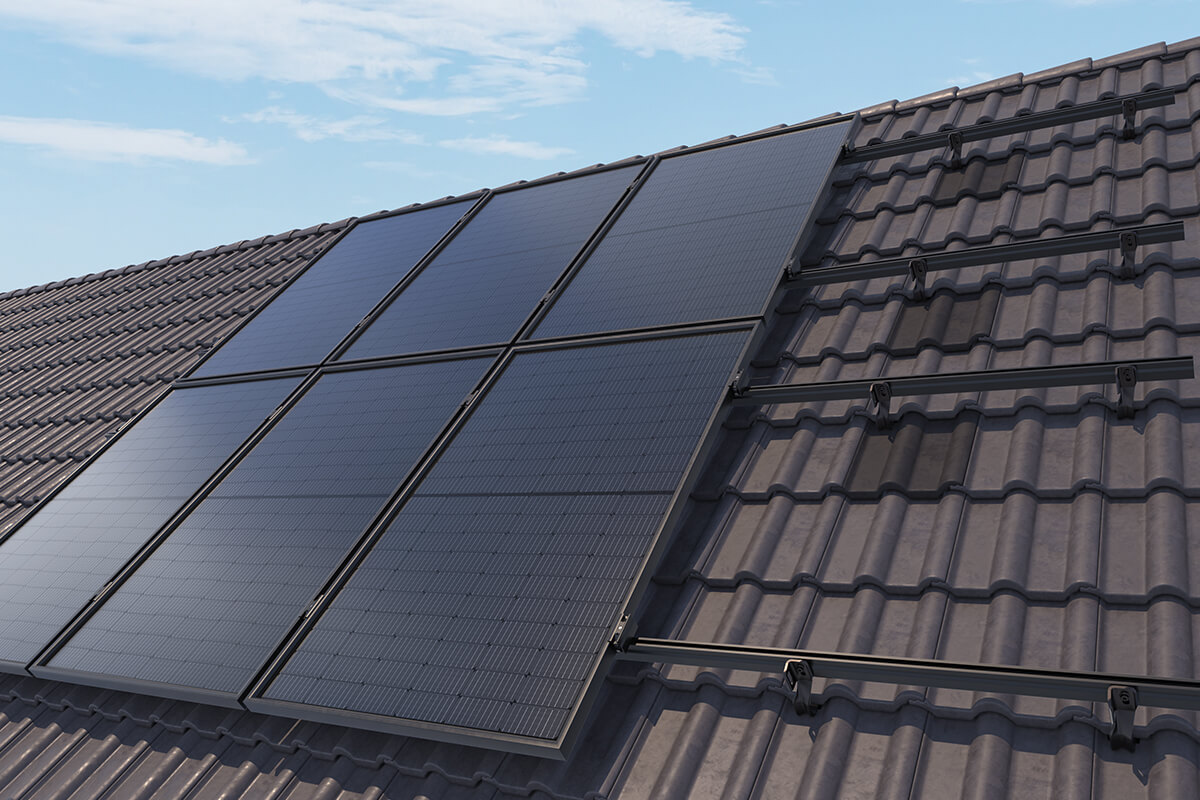
Always state-of-the-art.
High efficiency. Guaranteed. Thanks to the continuous further development and expansion of the IBC SOLAR module series, we can always guarantee very high module outputs and module efficiencies. We offer a performance guarantee of at least 25 years. And even after that, we stand by our responsibility in terms of sustainability. In Germany, for example, we work together with the waste disposal company Take-e-way, which takes care of proper recycling and recycles up to 95% of solar systems.
What are solar modules?
Solar modules, also referred to as solar panels or PV modules, are an elementary component of photovoltaic systems. They have the task to transform incident solar rays into electrical energy. In order to achieve this, solar modules are made up of several layers. Inside the panel are the solar cells. In each solar cell is a semiconductor, which is responsible for the conversion of sunlight into usable energy. Semiconductors have substances that develop electrical conductivity in light and heat, whilst having an insulating effect during cold weather. The semiconductors used in solar cells are doped differently. That is, various chemical elements have been added to them so that they are either positively or negatively charged. One speaks of p-type semiconductor layers and n-type semiconductor layers. If two differently charged semiconductor layers meet, a so-called p-n junction is formed at the interface. Here an inner electric field is formed. In the case of solar radiation, electrical voltage is produced and delivered to connected consumer devices.
On the cell layer is a layer of EVA (ethylene vinyl acetate) or cast resin. It protects the sensitive semiconductor against weathering, moisture and corrosion. There is also a protective layer below the solar module. This stabilizes the module structure and prevents stored heat loss. In order for the solar energy to be efficiently used, at least one of these layers must be slightly-permeable. A special solar glass plate is installed on top of the EVA layer. In order to achieve efficient energy production, these special requirements must be met: The glass must be thick enough to withstand wind and weather effects, and at the same time the incident light must not be absorbed and stored by the panel itself.
How are solar modules manufactured?
The production of solar modules and solar cells are based on the synthesis of silicon. Silicon is a component of sand or quartz and is therefore one of the most abundant substances on earth. With a degree of purity of well over 90 percent, silicon is considered a particularly pure substance. There are basically three types of solar modules: monocrystalline solar modules, polycrystalline solar modules and amorphous solar modules. These are different cell types and their differences can be traced back to the respective production methods.
Monocrystalline solar modules
In order to produce monocrystalline solar cells, the silicon oxide, which naturally occurs in the sand, is chemically reduced by the addition of carbon. This process takes place in a so-called arc furnace at a temperature of about 1.410 degrees Celsius. The result of this melt is a thin crystal rod, which is also referred to as a single crystal or monocrystal. The monocrystal is cut into very thin slices: with a thickness of 0.4 micrometers, the square slices are thinner than a human hair. The cut plate is called a "Wafer". After the wafer has been chemically cleaned, the doping takes place: At temperatures of 800 to 1,000 degrees Celsius, silicon atoms are replaced by atoms with a different valence. This increases the conductivity and thus the efficiency of the wafer.
Monocrystals are easily recognisable due to their dark appearance and rounded corners and have a particularly high efficiency due to their purity. Under ideal conditions this can be about 20 percent. Critics criticize the high energy expenditure required by the production of monocrystalline solar cells. Only after several years, such photovoltaic modules have a positive energy balance.
Polycrystalline solar modules
Polycrystalline solar cells are an alternative to monocrystals that are associated with a less complex production. In this method, liquid silicon is poured into prefabricated blocks and then cut into individual wafers. Here, they lose their single crystal structure, which is why they are significantly brighter than monocrystalline. Their efficiency is slightly lower at about 15 percent, but the simplified production process improves the energy balance and costs of manufacture.
Half-Cut modules
Half cell modules, so-called "Half-Cut" are based on crystalline solar cells, which are cut into two identical halves by means of a laser process after cell production. When such half cells are used, 120 instead of the previous standard number of 60 cells are used per module. By halving the cell, possible power losses are reduced and an increase in performance of up to 2.5 percent is achieved. Cell division also increases the total area of the intercellular spaces on the module surface. As a result, the module becomes slightly longer, but the width remains unchanged.
A further advantage of the HC module technology results from the string interconnection, which under certain circumstances and in comparison to standard modules, enables an increased performance with partial shading. The background is the use of 3 junction boxes which are placed in the middle of the module. This design allows a parallel connection of an upper and a lower string. If, for example, the lower area of the solar module is shaded in the morning hours, this will have less of an effect on the half-cell variant than on full-cell modules. For example, a half-cell module can still provide up to 50% of the total module output with partial shading. In addition, half-cell modules guarantee high reliability.
Amorphous solar modules
Amorphous solar cells are the most favorable variant. For their production, liquid silicon is evaporated onto a carrier material (e.g. glass). As a result, hardly any material is lost, and production and energy costs are comparatively low. The cells have an efficiency of about seven percent and are often found in pocket calculators and clocks.
From cell to solar module
For manufacturing a PV module, up to ten wafers are soldered with a copper ribbon. A so-called "string" is created. In order to achieve high performance, the individual solar cells should have the same properties. After the assembly, the cells receive the protective layer and the characteristic blue antireflection layer. At around 900 degrees Celsius, the cells are provided with contact strips from above and from below. These later ensure that electricity can flow. Once the solar module has been provided with an aluminum frame, a power test is carried out. On the basis of the results, the performance of the solar panel can then be classified before it is sold.
Which solar module is suitable for my roof?
There are several factors to consider when choosing a photovoltaic module. In principle, the roof should be checked before the installation as to whether it is sufficiently load-bearing. A solar module weighs up to 20 kilograms, whereas monocrystalline and polycrystalline solar modules are generally heavier than amorphous cells. The differing efficiencies of the various modules have already been addressed. With their high efficiency, monocrystalline solar modules are particularly suitable for installations in which a large amount of electricity needs to be generated or for small roof surfaces. This should at best be oriented towards the south, in order to ensure ideal exposure to the sun. If this is not the case, there is a loss of power generation, i.e. sun energy is lost. This risk is greater for monocrystalline solar modules than for polycrystals, which also function fully in the case of diffused solar radiation. In addition, polycrystalline solar modules are more cost-effective and have a high life expectancy of up to 30 years. They are therefore particularly suitable for the long-term production of solar power.